Comprehensive Overview: What is Porosity in Welding and How to Prevent It
Comprehensive Overview: What is Porosity in Welding and How to Prevent It
Blog Article
Porosity in Welding: Identifying Common Issues and Implementing Best Practices for Avoidance
Porosity in welding is a pervasive concern that frequently goes undetected up until it creates significant troubles with the integrity of welds. In this conversation, we will check out the key aspects adding to porosity formation, analyze its harmful results on weld efficiency, and review the ideal practices that can be taken on to minimize porosity incident in welding procedures.
Usual Sources Of Porosity
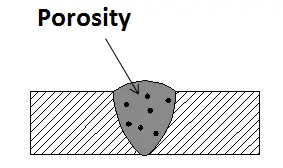
Making use of filthy or wet filler products can present pollutants into the weld, adding to porosity problems. To reduce these common reasons of porosity, thorough cleansing of base metals, proper securing gas choice, and adherence to optimal welding criteria are vital practices in attaining premium, porosity-free welds.
Impact of Porosity on Weld Quality

The presence of porosity in welding can significantly compromise the architectural honesty and mechanical residential properties of welded joints. Porosity produces spaces within the weld steel, weakening its general toughness and load-bearing ability.
One of the primary repercussions of porosity is a decline in the weld's ductility and toughness. Welds with high porosity levels tend to display lower effect toughness and lowered ability to deform plastically before fracturing. This can be particularly concerning in applications where the welded elements undergo vibrant or cyclic loading problems. Porosity can impede the weld's ability to effectively transmit pressures, leading to early weld failing and prospective you could try here security risks in critical structures. What is Porosity.
Finest Practices for Porosity Prevention
To improve the architectural honesty and quality of bonded joints, what specific steps can be carried out to minimize the occurrence of porosity during the welding procedure? Making use of the correct welding technique for the specific material being welded, such as readjusting the welding angle and weapon setting, can additionally stop porosity. Routine assessment of welds and instant remediation of any type of concerns identified during the welding process are necessary techniques to avoid porosity and create high-grade welds.
Importance of Correct Welding Techniques
Applying appropriate welding techniques is vital in guaranteeing the architectural stability and quality of bonded joints, developing upon the foundation of efficient porosity prevention actions. Too much warm can lead to raised porosity due to the entrapment of gases in the weld pool. In addition, making use of the proper welding parameters, such as voltage, present, and take a trip speed, is critical for accomplishing audio welds with minimal porosity.
In addition, the choice of welding procedure, whether it be MIG, TIG, or stick welding, should line up with the details requirements of the job to make certain optimal outcomes. Correct cleaning and preparation of the base steel, along with selecting the appropriate you could try here filler material, are also necessary parts of skilled welding strategies. By adhering to these best methods, welders can decrease the risk of porosity formation and create high-grade, structurally sound welds.
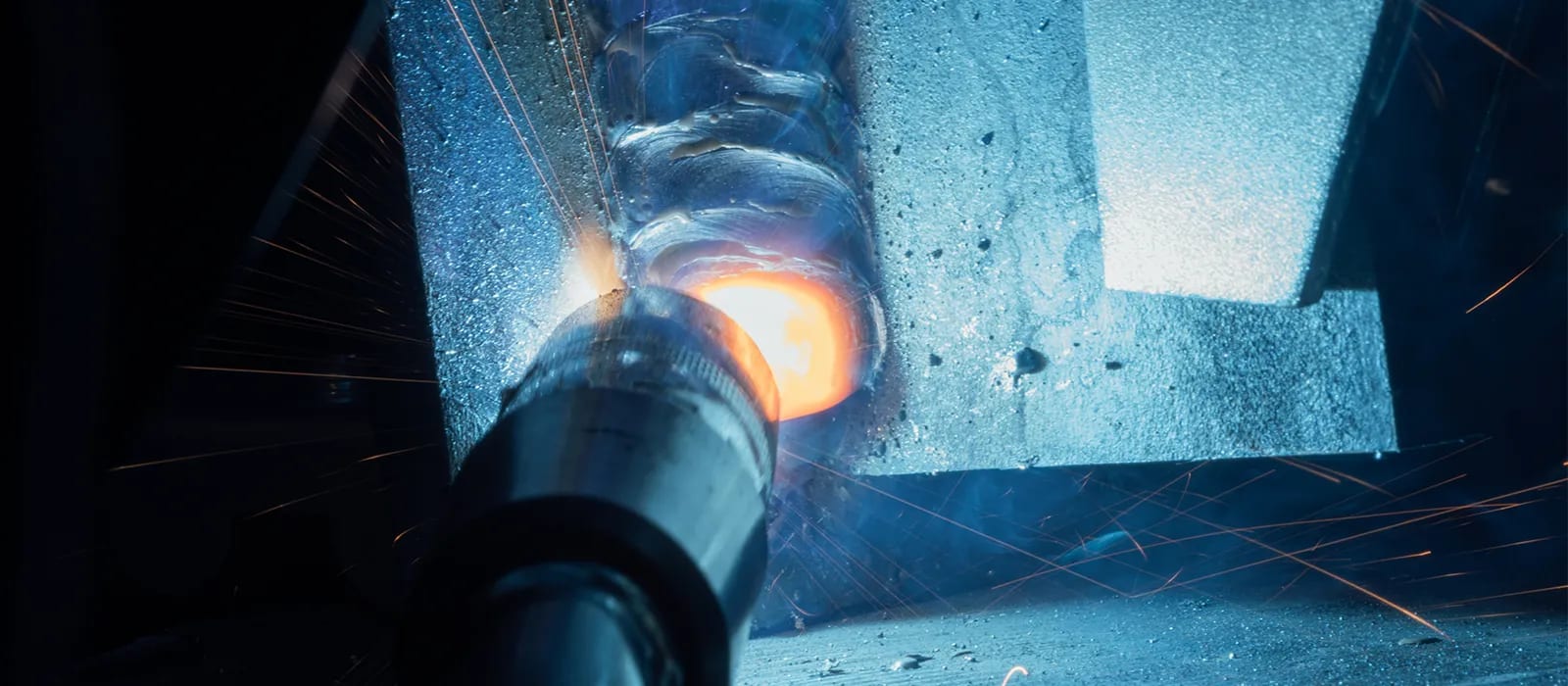
Testing and Quality Assurance Steps
Examining treatments are crucial to identify and prevent porosity in welding, making certain websites the strength and resilience of the final product. Non-destructive screening approaches such as ultrasonic screening, radiographic testing, and visual inspection are commonly used to recognize prospective problems like porosity.
Performing pre-weld and post-weld inspections is also essential in preserving quality control criteria. Pre-weld assessments involve validating the materials, tools settings, and cleanliness of the workspace to stop contamination. Post-weld assessments, on the other hand, analyze the final weld for any kind of defects, consisting of porosity, and validate that it fulfills defined criteria. Applying a thorough quality control plan that includes thorough testing treatments and assessments is paramount to decreasing porosity concerns and ensuring the general top quality of welded joints.
Verdict
To conclude, porosity in welding can be a typical problem that influences the top quality of welds. By identifying the common sources of porosity and executing finest practices for prevention, such as proper welding methods and screening steps, welders can ensure top quality and reputable welds. It is important to focus on avoidance approaches to decrease the event of porosity and keep the honesty of bonded frameworks.
Report this page